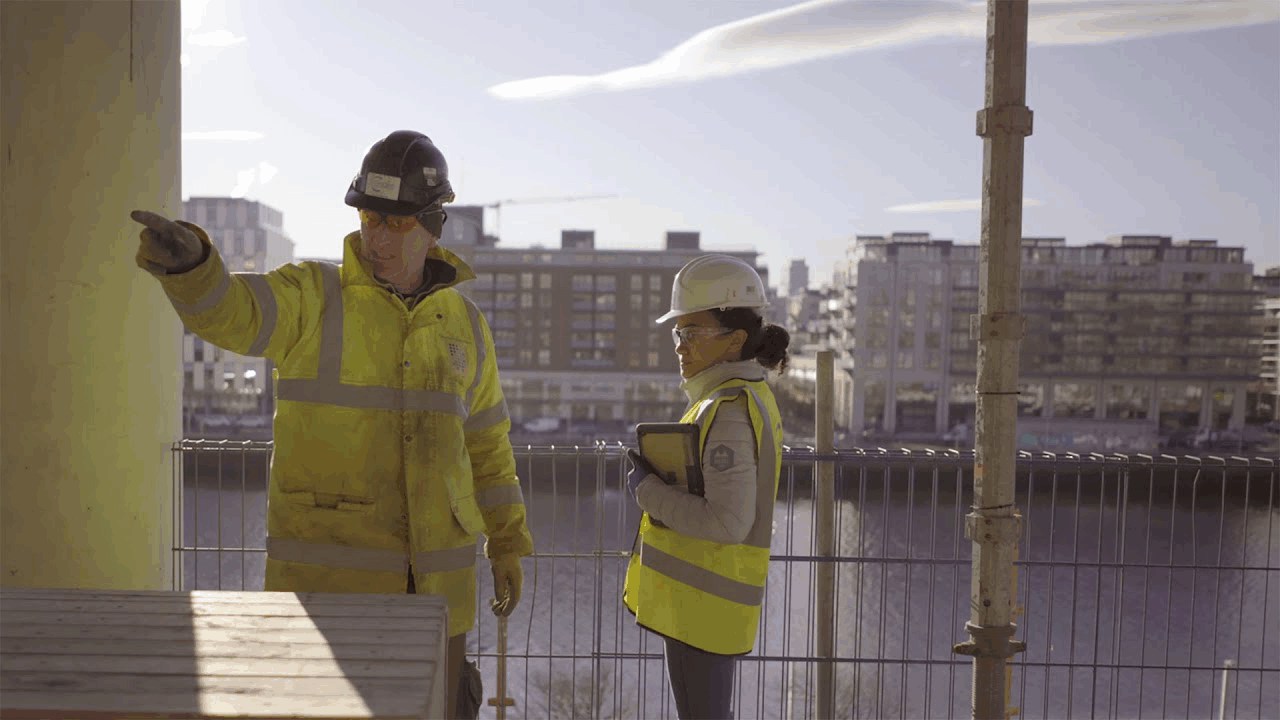
CEO Feargal Cleary started ClearTech Engineered Solutions in Dublin, Ireland, in 2010, at the depths of a major industry downturn.
Cleary knew that the traditional operations and models in design and construction would soon give way to technology-driven and environmentally sustainable models that would require leaner operations. While large companies shed workers and cut budgets to steady their businesses, Cleary aimed to build something smaller and more flexible: the first concrete post-tensioning service in Ireland.
Post-tensioning is the process of casting concrete with steel cables in ducts , then tensioning the cables to compress the cured concrete. The resulting slab has the compressed strength of concrete and the tensile strength of steel. This combined solution results in using significantly less concrete to achieve higher structural strength than traditionally reinforced concrete and pre-stressed concrete.
“Sustainability—it’s a big focus for ClearTech,” Cleary said. “So, what we do is we reduce the concrete depth, reduce the reinforcement, and this gives the client a sustainable solution over the lifetime of their building.”
ClearTech’s post-tensioning process has benefits for the environment and the company’s bottom line—not only in using less concrete, but in the form of tax incentives and rebates to lower the environmental impact of building.
With a decade of successfully delivering major projects, ClearTech remains a niche contracting business, with a small team of 20 full-time employees. ClearTech’s team punches well above its weight attracting high-caliber clients, however, thanks to its lean approach, which became possible when it put Bluebeam Revu at the center of its digital operations.
Digitizing estimation
In 2018, ClearTech’s project track record and strong reputation meant it was fielding more tender estimation requests than ever. Everyone was using PDFs for releasing design information, but there was no easy way to quantify material measurements digitally.
Furthermore, the ClearTech team was still using A3 and A1 prints, often losing half of a day waiting for designs to arrive from the printers, only to spend hours marking and measuring drawings by hand. This time-intensive process was also prone to errors, resulting in inaccurate estimations and rework. If ClearTech was going to respond quickly to RFQs, it needed to speed up its estimation process.
The team at Powergreen Digital introduced ClearTech to Bluebeam Revu. PowerGreen then trained the team on doing digital estimations with the automatic measurements and exportable metadata from Revu.
The results were almost immediate: The printing budget was cut by two-thirds, saving thousands of euros. And since proposals were less bogged down in administration, there was more time to look at new projects or refine processes.
It wasn’t long after that ClearTech started using Revu for other purposes. The team turned to digital document management, using Revu not only for designs but for all of its PDF documents. Now, everything that happens at ClearTech before going on a jobsite is in Revu.
Expanding use of Revu
The overlay tool in Revu was quickly discovered and put into constant use by ClearTech engineers in the design revision process. Designs change rapidly; tracking those changes and keeping every stakeholder aligned can be challenging because a single project might have hundreds of different designs. ClearTech engineers use overlay tools in Revu to compare plans and quickly spot design differences.
Leticia Siqueira, a ClearTech structural engineer, uses the overlay tool to track the change that happens onsite and at the construction stage. “So, when new revisions come in, I can easily see the difference and work on them straight away,” Siqueira said.
“We used to print the two drawings—the newest one and the previous version—and look at them,” added Thiago Tamm, another ClearTech structural engineer. “It would take well over half a day to go through these drawings to compare changes. But, with the overlay tool, you can just do it now in fewer than 25 minutes and you’re done with comparing.”
“We want to be a leading light in the industry, and we’re pushing the likes of Bluebeam to demonstrate there is an opportunity for innovation in the industry here in Ireland”
Feargal Cleary
CEO
ClearTech
Using the overlay tools, engineers can also share revisions almost instantly, creating a trustworthy and up-to-date single source of truth for all parties, increasing transparency between stakeholders. Communication between the office, jobsite and contractors is also faster, simpler and more precise. The benefit comes in the form of cost savings by minimizing delays and mitigating risks for rework and injuries, as fewer hours are necessary to complete a job.
“We have the cloud-based system so that we can communicate with the guys on site,” Tamm said, referring to Bluebeam Studio. “We are always making sure that the newest drawings are in there for them to follow the current revision.”
Siqueira added that Revu helps her track “any change that happened on site, and to communicate in an easier way, in a personal way as well, with all our employees and other contractors.”
ClearTech also uses Revu to set key performance indicators (KPIs) for engineers on site to track how long each task requires, as well as to input that data into custom column sets in Revu. By analyzing this information, ClearTech can more accurately estimate the cost of labor as well as that of concrete and steel in subsequent budgets. They even task its on-site engineers to complete work in less time, which has a measurable impact on the company’s bottom-line.
Every project’s completion adds data to the company’s business intelligence, so ClearTech can continually refine and improve its operations and estimates and reduce waste in both material and wages—all of which fits the company’s larger lean approach.
Cleary said that by “using customized columns … we’re able to get accurate understanding of what we’re using on site, what’s being used, what’s required and what we need to order. We use that insight in the office to create our orders to look ahead.”
Because Revu is at the center of ClearTech’s data operations, it’s also used for the company’s QA/QC processes—partially for its own meticulous record-keeping but also in fulfillment of an Irish legal requirement, the Building Control Amendment Regulations (BCAR). The regulation requires tracking materials used in building and renovations, and is designed to increase transparency between builders, owners and residents.
“It’s important that, through the BCAR, we have an accurate understanding of every part of the systems that we’re putting into the concrete,” Cleary said.
There’s also the advantage of better communication with partners and clients. “The other companies that we work with, they use Bluebeam as well,” Tamm said. “And we communicate using the same software so we have more concise and accurate comments and reviews on the drawings.”
Cutting waste, saving money, expanding frontiers
Since ClearTech started using Revu for its estimations, it has cut waste, improved record-keeping and communication and increased transparency among stakeholders.
Since adopting Revu, ClearTech has won an additional 50% of projects, thanks to its much-improved estimation and communication process. The company has also gone on to complete work for clients such as Salesforce, Facebook and Amazon.
Still, the most important difference might be cultural, as the entire ClearTech team has used the technology to improve its performance, raising the company’s ambitions.
ClearTech has since taken its business international, completing projects in Saudi Arabia, Vietnam, the Philippines, Malaysia and Indonesia, where it recently opened an office to focus on growing its business in the region.
Growing the business at home, to be sure, has also become a bigger priority.
“We want to be a leading light in the industry,” Cleary said, “and we’re pushing the likes of Bluebeam to demonstrate there is an opportunity for innovation in the industry here in Ireland.”
Today, ClearTech is faster, leaner and more successful than ever. It has become the company that Cleary envisioned when he first started it 10 years ago.
“What we’re seeing now is that we can think ahead and we can look forward and that there’s a consistency of projects that are coming in now that we didn’t have before,” Cleary said. “And that’s what we are seeing now that we’ve started to use Bluebeam.”